Five Tips on Value Engineering Terrazzo Flooring into Your Construction Budget
Commercial flooring is a significant undertaking and represents a considerable chunk of the construction budget. It has to look good and perform well long term. Striking a balance between costs, functionality, and aesthetics can be challenging.
“When everyone sits down to discuss the construction budget and decide what will be included, architects who are familiar with terrazzo typically are rooting for it,” said Mark Naugle, President of Steward Mellon Company in Tampa, Florida.
The choice of terrazzo is clear for many architects, whose preference would naturally be a floor that offers unbeatable performance on every metric, from life-cycle costs to durability, strength, and crack resistance. It brings exceptional value to the end-user. It’s seamless—no grout joints—and nonporous, so it’s simple to maintain. A terrazzo floor’s longevity will match that of the building in which it’s installed. In case of a hurricane, terrazzo may even outlive the building.
There is no debate that terrazzo is a versatile, poured-in-place product that provides many options to meet the needs of any situation and budget. So how can you hope to get a terrazzo floor specified in the project, at the right cost?
Here are five guidelines to bring the price in line with a terrazzo installation:
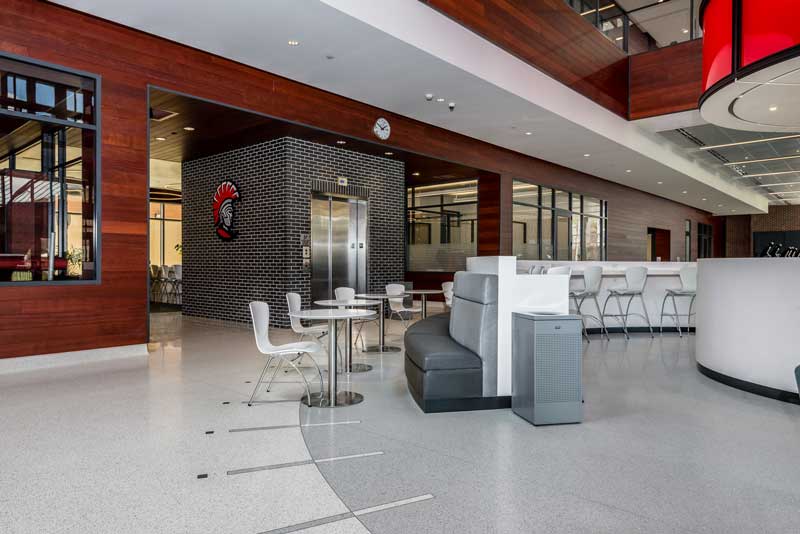
University of Tampa Fitness Center
1. Think Big
Low performance doesn’t always equal lower costs, even in the initial installation, especially on large jobs. Large-scale terrazzo jobs can be more cost-effective than many lower-performing options.
When comparing a terrazzo floor to manufactured options, check the product literature carefully for warrantee and life cycle data to avoid unpleasant surprises. Also, take a look at the installation requirements of the flooring under consideration. What money you may save might not be worth what you’re giving up.
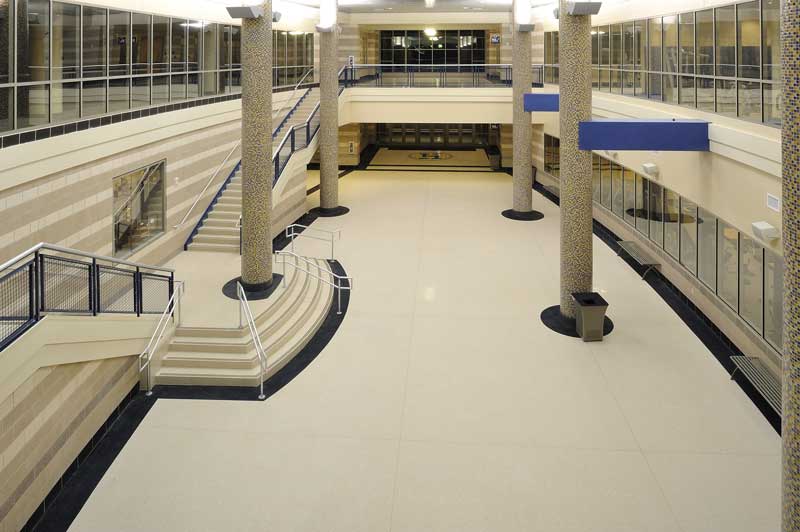
Holy Cross
2. Keep it Simple
Keeping the design to a single-color matrix is just one of many options to reduce the cost of a terrazzo installation. Price can vary greatly depending on the complexity of the design. With epoxy terrazzo, Naugle recommends installing strips 10-25 feet apart and coordinated with substrate joint locations. Another option for high impact at a reasonable price is accenting a neutral-toned floor with a colorful medallion.
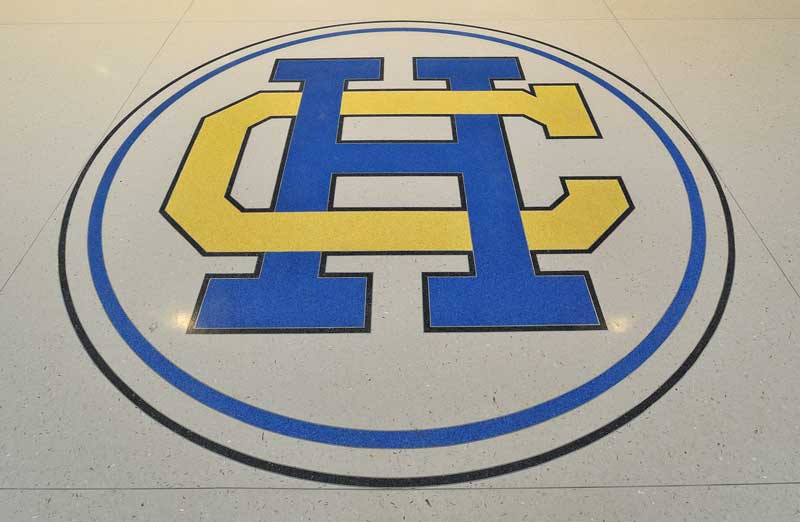
Holy Cross logo
Significant price variations are also found in aggregate choice: 100 percent marble aggregates are a cost saver. Aftermarket finishes at additional cost may be proposed but are not necessary for a high-performance floor.
When bidding against a soft flooring product for a school, for example, Naugle advocates that the terrazzo scope be set at a one-color floor with marble aggregate, maybe a logo in the entrance, and carry the same base and stair finishes as the soft flooring in the base bid. This comparison allows the value of a poured-in-place terrazzo floor to come to light.
3. Strategize Prefab Options
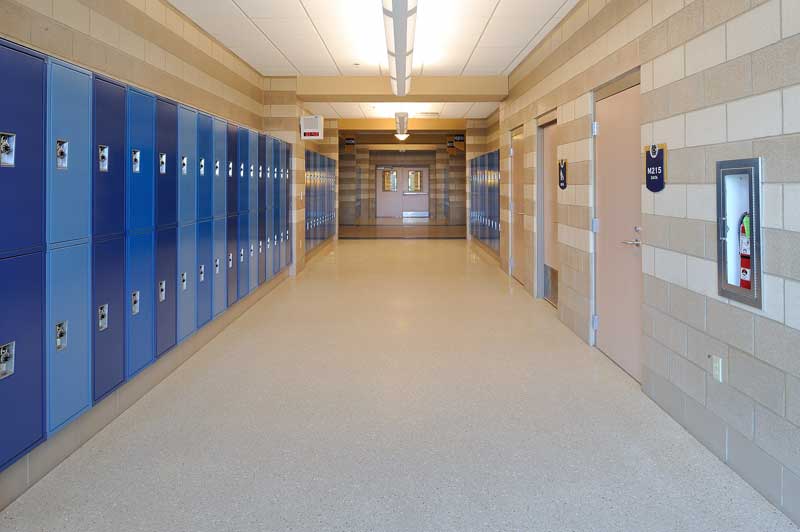
Holy Cross hallway
Knowing when precast terrazzo makes the best sense is another key to lowering costs. In small areas such as mid-stair landings and elevator cabs, precast may make more sense than engaging installers in the multi-step process of pouring terrazzo on-site on a small scale.
Making small concessions in the design can help bring the project within the target price range. Instead of a terrazzo base, exploring other material options may be another way to work down the bottom line. You can get a lot of poured-in-place floor square footage for the price of terrazzo base, Naugle noted. Installing a precast base at a later date is always an option. It’s a quick, clean install after the existing finishes are removed or have worn out and can still match the adjacent floor–“a conversation worth having.”
4. Compare the Timeline
Your project may see upfront savings when your terrazzo contractor can get the materials on the job quicker than a manufactured product, especially for a project of significant size. Many manufactured products that resemble terrazzo have extended lead times with production and shipping. The resin and aggregate can typically be on-site within a few weeks with terrazzo. If the design team decides to add terrazzo scope throughout the course of the project or needs to make design changes late in the game, the material is available.
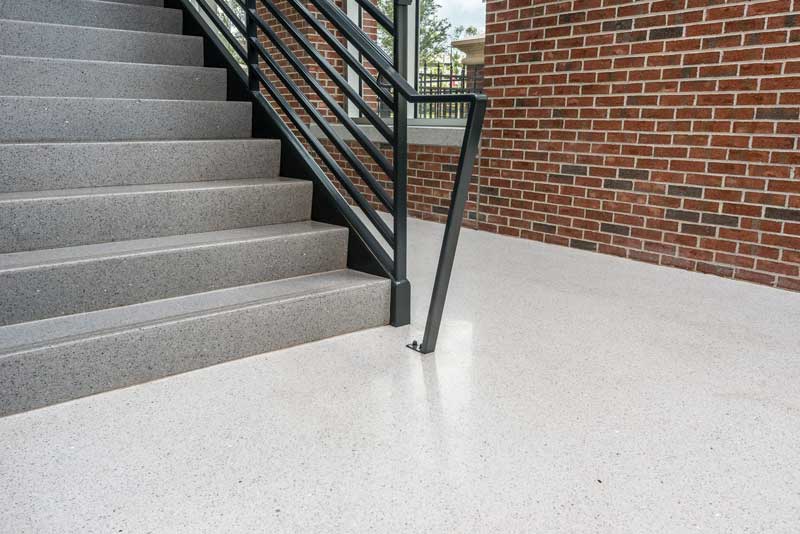
University of Tampa Fitness Center
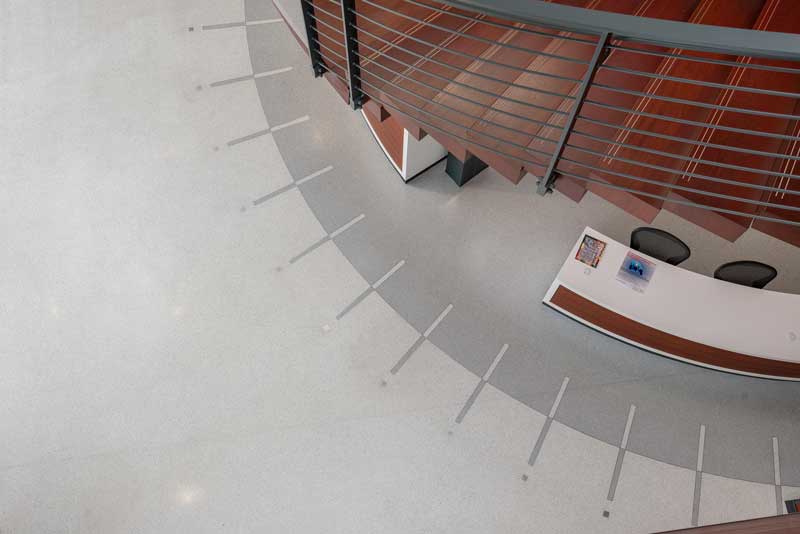
University of Tampa Fitness Center
5. Count the Value
A terrazzo floor offers numerous advantages that can figure in the final accounting. The potential to extend the life of an original terrazzo floor over 100 years versus materials that will be up for replacement far sooner brings considerable value to the owner. The cost-effectiveness of maintenance is another significant advantage of a seamless, impermeable floor.
“There is always a way to value engineer terrazzo in,” Naugle said. “The beauty of what we do is that we can get the price in the ballpark, especially in light of the value it brings.”