The Reputation vs. The Reality: Seven Keys to Grief-Free Installation Terrazzo’s reputation of hand-crafted luxury has been solidly built on the traditional sand cushion, cement-based terrazzo still found intact in historic structures around the country after 100-plus years. It’s logical to assume that such a high-end finish won’t come cheap or easy. Its life cycle beats carpet by decades, but unlike carpet, it can’t just be dropped in at the end of construction. It’s the kind of reputation that can cause a general contractor to assume the worst about what a terrazzo installation is going to do to the cost and scheduling of their jobs.
While today’s generation of terrazzo is still poured-in-place on the job site, and as durable as ever, its reputation has lagged far behind the reality of the industry. The evolution of the installation process has come a long way since those century-old floors were first installed. And with these advances, comes very good news for the GC in terms of costs, time, space and headaches.
First, installation has become simpler, cleaner and cheaper, while terrazzo’s design capacity has expanded exponentially. Over recent decades, the terrazzo industry’s large-scale shift to epoxy from traditional sand-cushion has dramatically lowered costs while playing a key role in the several game-changing improvements in the process.
We asked several GCs who are experienced in working with today’s terrazzo, along with a veteran terrazzo contractor, to share their insights on the challenges a GC faces and their top advice for trouble-free terrazzo.“The product has a certain way to install it, and as with any trade, there’s a cost and a mess involved,” said Henry Serry, an experienced construction manager and President of Koontz Corporation, Inc., of San Antonio, one of the city’s largest general contractors. “You just have to understand and plan for it.” What exactly does a GC need to know and do to minimize disruption and delays while integrating terrazzo into a project?
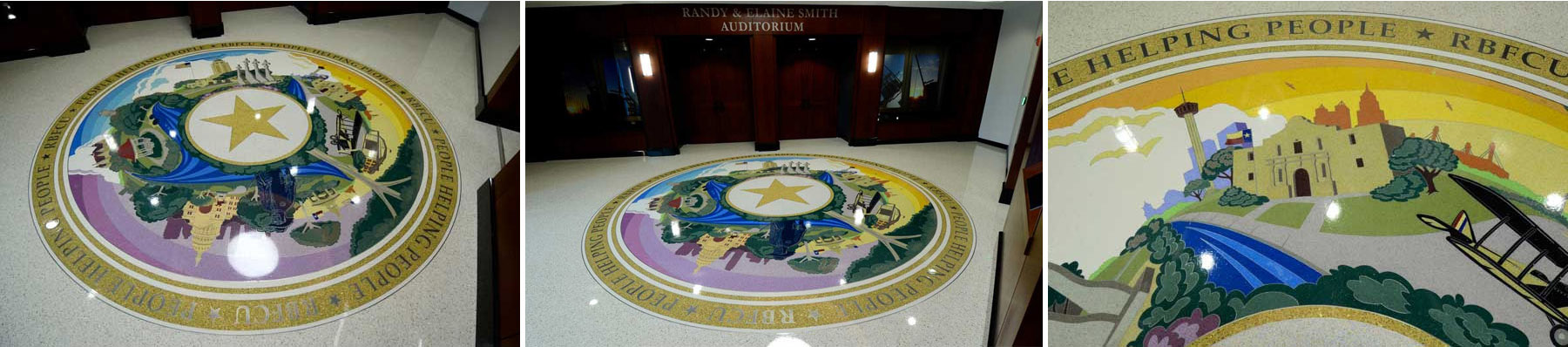
Brett Dunlap, a Senior Project Manager with JE Dunn of Eden Prairie, Minn., is experienced in working with terrazzo on large, multidimensional projects. In 2014 he completed a $70 million reconstruction of University of Minnesota’s Northrop Auditorium, involving a total 44,000 square feet of various terrazzo systems, from three-inch sand cushion to three-eighths-inch epoxy thin set. Also restored was 10,000 square feet of 85-year-old traditional sand-cushion terrazzo. Mr. Dunlap condensed his top recommendations to the GG.
“If planned for appropriately the terrazzo work can be incorporated into the schedule efficiently,” Mr. Dunlap advises. “Allow adequate space for the placement of the material, allow adequate schedule, ensure sub-base prep is completed properly and control access over finished areas.”
Digging deeper, let’s look at the specifics of how to accomplish those recommendations, with the help of our experts, starting with exactly how much space terrazzo installation requires.
The Seven Keys to Grief-Free Installation
Key #1: The bigger the space, the quicker the pace
“The terrazzo contractor is going to occupy the space sooner or later, but the quicker we are in and out the better off we all are,” said Joe Iorio, Project Manager with Yorie Tile & Terrazzo, Inc., of Allentown, Penn., and a member of the National Terrazzo & Mosaic Association.
Mr. Iorio knows how to work with the GC to expedite a project and shared his specific strategies to speed up an installation. In 2015, for example, his crews installed 4,000 square feet of epoxy thin set, working nights and weekends, in just 10 days. Installed in the Verizon Building in downtown Philadelphia, the classic design of the modern materials make it a perfect match for the 1903 structure. “Allowing adequate scope is the key to turning the job over quickly,” Mr. Iorio advises. Giving the terrazzo installers adequate square footage to use manpower wisely and maximize man hours per day is the first key to accelerating the process.
“It’s not a manpower issue, it’s a cure time issue,” Mr. Iorio explains. Because of the time terrazzo takes to harden, restricting crews to smaller spaces in order to keep other trades working in those areas only slows down the process by slashing hours off full days of manpower.
If, for example, the GC tries to parcel out a 10,000-square-foot job to the terrazzo crews in 1,000-square-foot increments, costs escalate. An installation of 1,000 square feet will take just as long as 2,500-3,000, which a terrazzo contractor can turn over in about ten days, depending on the pattern and substrate conditions.
Mr. Iorio said he always presses GCs to allow them a scope of at least 2,500 square feet; it’s worth the tremendous savings to the schedule. When even more is space allotted, the terrazzo crew can get in and then vacate the area even more quickly, he explained.
Being able to occupy 5,000 square feet unrestricted pushes the schedule ahead dramatically, Mr. Iorio said, noting that once he sits down with GCs to show the difference, they are always on board.
“GCs are amazed how much time it shaves off—20-30 percent of working days,” he reported.
Key #2: Trade talk: sequencing teamwork
Terrazzo installation is highly predictable process because it’s a repetitive system with equal increments, Mr. Iorio stated. “That’s the beauty of terrazzo: your forecasting ahead to schedule is simple.”
While Yorie Tile & Terrazzo installs tile, terrazzo, epoxy floors and marble, Mr. Iorio states that among those finishes, “terrazzo is actually the most user-friendly for the GC, with the proper scheduling.” While noting that the challenge of scheduling a terrazzo installation can’t compete with the ease of VCT, he ranks it among class-A lobby space finishes with stone slab or marble tile.
The first line of defense in protecting finishes is well-planned sequencing. Experienced general contractors shared their recommendations for successful scheduling.
“When sequenced properly, installing terrazzo is no big deal,” said Henry Serry. He emphasized the need for conversation between the GC and the terrazzo contractor before the job begins about the requirements of the installation within the project as a whole.
Mr. Serry managed an award-winning terrazzo installation in Randolph Brooks Federal Credit Union’s San Antonio headquarters, with terrazzo contractor Venice Art Terrazzo Company of San Antonio, in 2013. The focal point of the 9,800-square-foot installation is a 16-foot pictorial medallion depicting iconic images of Texas history. The design is exceptionally complex, integrating 54 colors of epoxy terrazzo.
The medallion alone required a couple of months’ work, Serry recalled. There was no way around planning for the time needed to allow the terrazzo crew to fully occupy that space.
Mr. Serry explained that proper terrazzo installation is highly “project dependent, even room dependent”: installing it requires close attention to what trades go in before and after the terrazzo itself. For installing finished millwork, wood panels and doors, for example, time should be allowed at the end.
Justin Boehm, Senior Project Manager with DE Harvey Builders in Pearland, Texas, seconded Mr. Serry’s recommendations. He encourages GCs and terrazzo contractors to put their heads together and include other subcontractors in coordinating all the variables, from space and timing to access to and from and around the terrazzo installation.
Key#3: Cracking the case of the substrate
“Terrazzo is a veneer system; it reacts to whatever the concrete substrate does,” Mr. Iorio cautions. Standard terrazzo installation includes a crack-suppression membrane over the slab to inhibit cracks in the substrate from telegraphing through the terrazzo, but whatever panels or expansion joints the substrate demands, those must be taken into consideration in the terrazzo design.
Communication between the various trades is, again, therefore, essential to the smooth progress of project featuring terrazzo installation.
“The GC and the terrazzo and concrete contractors need to have a good solid meeting two to three weeks before pouring any concrete,” Mr. Iorio cautioned. “It’s well worth the hour conversation. It saves a lot of grief and the final result shows the coordination.”
With epoxy terrazzo, divider strips serve purely for aesthetic purposes, as Mr. Iorio explains. Because of shrinkage in cement based terrazzo, on the other hand, it requires 4×4 or 5×5 panels. To minimize unnecessary disruption to the terrazzo design, the architect or structural engineer may need to be involved to gracefully coordinate the pattern with the substrate joints.
All parties concerned need to reach clear agreement about expectations for flatness and all substrate issues, with any needed adjustments made to the plans, he cautioned. Particularly with renovation projects, if trenching of the concrete is necessary, for example, that’s a conversation GC needs to have with both contractors.
Key #4 Plan for Less Mess
In the minds of many construction industry professionals, terrazzo has still not quite shaken its old reputation for dumping an extremely messy installation process on a project. Several particular changes in the industry merit a radical upgrade in this part of terrazzo’s reputation, though. Over the past 20 years, terrazzo installation has become a vastly cleaner process with numerous improvements in the process and the equipment, Mr. Iorio reports. The greatest progress has come in advances in the diamond stones or pads used for grinding. The quality of grinding has reached a peak in effectiveness today, Mr. Iorio reported. The massive industry shift from cement-based terrazzo to epoxy terrazzo, which has lowered costs considerably, has also played a major part in transforming the installation process.
Grinding just 100 square feet of cement sand-cushion terrazzo in previous decades would generate a 50 gallon-drum of slurry, while even in the earlier days of epoxy terrazzo, the grinding process would generate just one-quarter of that amount of waste. Today’s improved grinding equipment has allowed installers to double to 800 square feet the square footage of epoxy installed per 50-gallon drum of grinding slurry generated.
Concretely, the numbers add up to a far more streamlined, less labor-intensive process. These advances and reduction in mess benefit the entire project.
In addition, most terrazzo contractors dry grind now. Polishing is now the only step his company grinds wet, Mr. Iorio reported, noting also that in spite of the sound of it, the amount of dust generated with dry-grinding is minimal.
“Dry grinding has saved a lot of grief,” he declared. Improved diamond equipment has not only rendered terrazzo more user-friendly for all concerned, but it has also improved the appearance of the terrazzo, Mr. Iorio added. The luster of historic terrazzo floors earned only by age is achieved instantly with an epoxy floor.
Key #5 Protection Goes Both Ways
Proper protection of finishes, including the terrazzo itself, is essential to successful installation of terrazzo. While proper sequencing can eliminate the bulk of potential damages of installed finishes, as Mr. Boehm observes, installing terrazzo does take more planning than carpet or tile. Plastic sheeting taped around the work area to protect wood, glass and drywall can head off many a heartache, he advised.
A perhaps less obvious problem arises when terrazzo falls victim to its own sterling reputation as an indestructible finish. While terrazzo is exceptionally durable, floor protection after installation is still a must, Mr. Iorio said.
He reported that he sees GCs protecting other solid-surface floors, but sometimes assuming that terrazzo is relatively invulnerable.
“I’m not asking for more protection than for other finishes,” Mr. Iorio explained, “but we can’t have masons rolling pallets over it.”
If terrazzo is protected properly after it’s completed, such as by laying down plywood sheets over it, work can continue above it two days later, against 30 days for floor tile, according to Mr. Iorio.“That’s a considerable benefit to the back end of the schedule.”
Key #6: Hire only NTMA contractors
The quality of workmanship and reliability of subcontractors are perennial concerns for the GC. The best way to ensure a quality terrazzo installation is to engage a contractor who is a member of the National Terrazzo & Mosaic Association (NTMA).
Membership in the NTMA is limited to contractors who meet rigid proficiency standards and participate in educational seminars conducted annually by the association.
Furthermore, working with an NTMA member allows the GC access to the expertise of NTMA’s full-time technical department, with some of the best experts in the industry. The association also offers recourse in case of any dispute, conflict or concern if the NTMA member’s work comes into question. Material suppliers are also vetted through associate NTMA membership for those whose products comply with the association’s standards.
Key #7: Reasonable and rewarding
Terrazzo has come a long way, and with the right approach and informed expectations, a terrazzo installation can bring GCs a higher return than ever on their investment in it.
“Terrazzo is a fantastic product, a high-end product, a permanent product. I enjoy terrazzo jobs because it results in a high quality project,” said Mr. Serry. “It reflects well on me and challenges me to do it well.”