What Design Professionals Need to Know
A true terrazzo floor is like no other flooring material. Its raw materials are assembled on the construction site and poured in place by hand as an integral part of the structure. Terrazzo is an exceptionally versatile product, with options to adapt to any project’s demands.
Yet with a poured-in-place floor, it can sound like an out-of-your-control process. What will the finished product look like? What are the options? How is the quality controlled?
These questions were addressed at a preschool center in Atlantic City, NJ. They initially planned to install manufactured ultra-thin terrazzo-style tiles, but through an educative process of negotiations, they opted instead on terrazzo.
“The architect was thrilled,” said Michael Blackburn, president at Master Terrazzo Technologies in Washington, DC. “Poured-in-place terrazzo gave them all the advantages for less money—a faster, less expensive option for a higher-performing product.”
What’s so great about pouring in place? Experts point out several critical advantages of a poured-in-place floor over manufactured products, whether porcelain tile, terrazzo-style tiles, or soft flooring products.
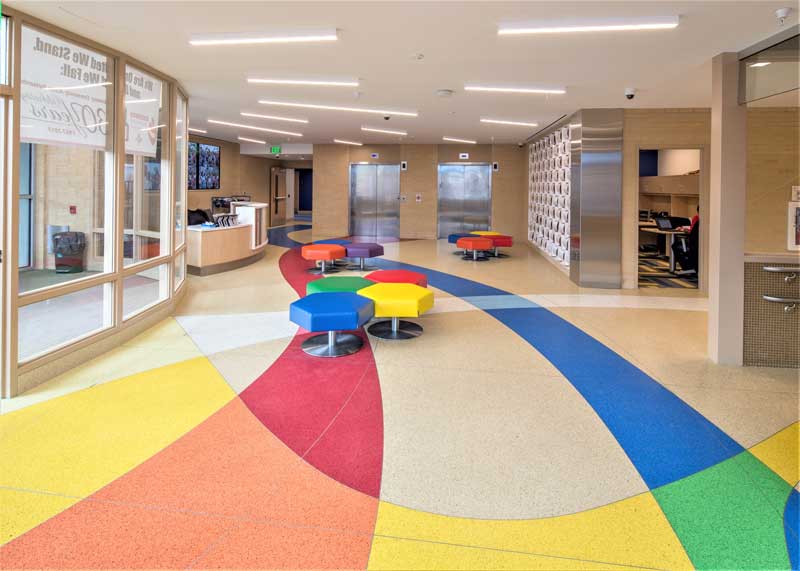
Seamless Floor
The nature of a poured-in-place floor provides a host of benefits. By every metric, the performance of a poured-in-place, thin-set epoxy is unbeatable: its durability, compressive and tensile strength, the capacity to bond to concrete, and crack resistance. It is the leader of life-cycle costs and a life-of-the-facility finish. A resilient, monolithic surface, terrazzo is simpler and cheaper to maintain and keep clean than any other flooring.
Manufactured options, on the other hand, labor under the disadvantages of joints—weak spots that can harbor dirt and bacteria—or the absorbency of carpet. A close look at product literature and warranties and a visit to an installation or two of such alternatives can illustrate this point.
Control Within Flexibility
As with other manufactured products, the aesthetic options of a terrazzo installation are established through samples. NTMA contractors can quickly provide custom samples and can match any color on a paint fan or from another product sample or existing finish.
One misconception with manufactured products is that they offer machine-produced consistency. Michael LaMontagne, AIA, principal architect with C&S Companies, explains why this is not necessarily the case.
“I learned that with ultra-thin tile, there’s no guarantee of thickness to a certain dimension,” said LaMontagne, who has found significant differences in them. “It can cause issues if you are setting it in a bed and dealing with a ⅛-inch difference in the tiles.”
According to Blackburn, many manufactured products also require a stringent minimum substrate tolerance of ⅛-inch in 10 feet. Such a standard can typically only be achieved with a flowable self-leveling product. When this requirement is discovered after the package is brought out, it can add time and cost.
A poured floor allows greater control and flexibility on site, to adjust to site conditions and project demands, noted Joe Iorio, president of T. Yorie Corp. in Allentown, PA. NTMA contractors are well accustomed to such circumstances. They might include opening up a pattern a little to marry with the ceiling soffit, accommodating last-minute design changes, or the option of bending divider strips by hand on the job site.
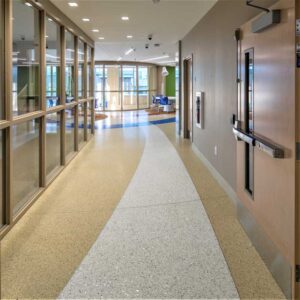
Terrazzo Hallway
Speed & Cost
A key factor that can bring the price of a poured-in-place floor below that of ultra-thin tiles is the complexity of the patterns. Manufactured products generally have to be outsourced to a waterjet contractor to achieve intricate designs, which is costly and impedes further changes to the designs on the job site.
A poured-in-place floor allows for divider strips to be bent by hand. In the case of the preschool in Atlantic City, the tiles were expensive, and then the waterjet costs were so high that a handcrafted terrazzo floor was clearly a better value.
Raw materials can often be on site more quickly than manufactured products, which may have extended lead times with production and transit. With terrazzo, the resin and aggregate can typically be onsite within a few weeks.
The Right Contractor & NTMA Support
Working with a member contractor of the National Terrazzo & Mosaic Association (NTMA) is the surest route to achieving a quality installation. Confidence in the process can rest on the contractors’ proven competence in their craft, attained only through training and experience. In order to join the association, each member is subject to a rigorous selection process and set of requirements, ensuring the contractor will be a steady, experienced guide in the process.
Furthermore, the NTMA serves as a reliable, authoritative third-party resource as needed for all players in the project. Technical Director Gary French provides guidance and support for the asking. Assistance on terrazzo projects is available, free of charge at (800) 323-9763, ext. 1 or at tech-info@ntma.com.