Role of the Machine in an Industry of Hand-Crafting
When terrazzo installers were in the midst of work on the public art installation that was to become the National Terrazzo & Mosaic Association’s 2019 Job of the Year, the general contractor asked them to expedite their timeline on the job site. The terrazzo contractor had a sure solution: switch from hand-bending the intricate divider strip patterns onsite to having them prefabricated by a strip supplier. That shift shaved a month off the six-month schedule.
“As a bonus, making this switch provided the installation with considerably higher quality on the divider strip installation,” said Eddie Lourenco, president of Associated Terrazzo of San Francisco.
The 20,000-square-foot “Secret Garden” in epoxy terrazzo in the grand hall of the Salesforce Transbay Transit Center in San Francisco features super-scaled flowers, birds, insects, and abstract shapes in 16 colors. Embedded in the floor, which was installed over a radiant heating system, are 375 hand-bent and waterjet-cut elements of brass and zinc. The contractor installed another 6,000 square feet of single-color terrazzo elsewhere in the terminal, including five precast terrazzo staircases and 11 elevator cab floors.
The intricate divider strip patterns were primarily bent by hand, with some waterjet cut, by Manhattan American Terrazzo Strip Company. Designs were created in sections and soldered to expanded metal lath panels, many as large as 11’x7’. They were delivered to the construction site, where the crew assembled and aligned them on the floor.
Fab Prefab
Prefab and modularization of terrazzo, from precast epoxy terrazzo components–base, stairs, and stair components– to vertical panels, floor design elements, and divider strips, contribute significantly to terrazzo’s flexibility to meet the demands of a given project. In 2020, about one-third of the entries submitted to the National Terrazzo & Mosaic Association for judging in the Terrazzo Honor Awards program included prefab elements.
Prefab and modular construction is a long-familiar concept; precast terrazzo elements were in common use and considered to offer superior quality already in the mid-1920s. Today, BIM and green building are driving a new look as an ever-improving solution to construction challenges.
An element of resistance to modular materials and prefabrication is traditionally rooted in a perception that they compromise quality. As in the Transbay Transit Center example, however, prefab strips can provide an excellent result.
Prefabrication of divider strips includes both the bending of strips by hand in metal shops and the use of a highly-advanced waterjet–a precise, computer-controlled cutting machine. Both techniques have roles to play.
“Hand bending of strips by highly-skilled people helps keeps the art in terrazzo,” said Barry Austin, General Manager of Manhattan American Terrazzo Strip Company. “That, coupled with waterjet cutting, results in designs of exceptional quality.”
Bottom Line Bonuses
The potential of prefabrication and modularization to increase productivity and ROI on a construction job is demonstrated in a McGraw Hill Construction study about ten years ago, which called on owners and architects as essential in driving the successful specification of such elements.
Overwhelmingly, the study found that the introduction of modular elements served to tighten project schedules. Over 20 percent of all cases were expedited by a month or more, as at the Transbay Transit Center. Furthermore, two-thirds of the projects studied reported decreasing budgets by at least six percent in over 40 percent of the instances. Most reports were that bringing in ready-to-install elements decreased construction site waste by five percent or more in close to half of the cases.
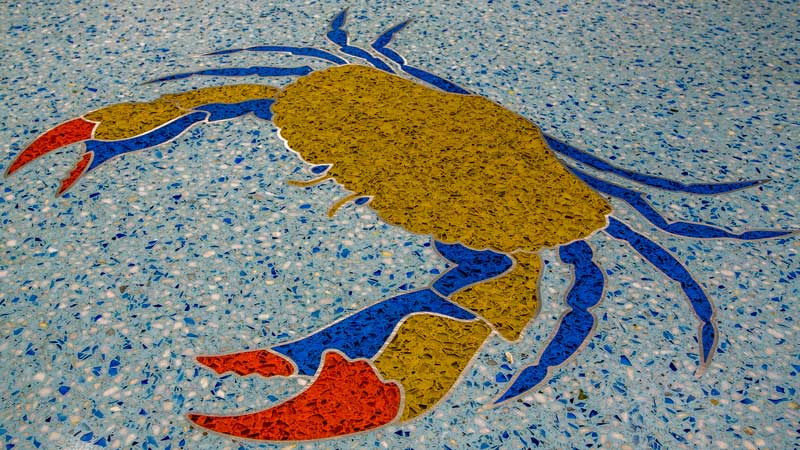
Speed is Money
On a terrazzo project, prefab strips are an option that streamlines the installation process on the job site, according to Russell Day, National Sales Manager with strip contractor National Metal Shapes.
“While strips and expansion joints can be hand-laid onsite, a prefab company is at the ready with the material and size specs needed,” Day said.
Prefab strips reduce time in the field and thus obstruction of other trades. They also lower the chances of miscalculation and bring a measure of control in the risks taken. It can mean one less complicated process taking place in the thick of the action, one less thing to go wrong in the field.
Shortage of Skilled Labor
With labor as a high cost in any construction budget and skilled labor now at a premium, strategic use of in-shop fabrication or machine production can be a powerful force in making the most of that precious commodity. While terrazzo installation is highly dependent on experienced technicians’ handcrafted skills, there’s a place and time for letting the component specialists do what they do best. Conserving skilled installers’ time for tasks that only they can take on may boost big-picture productivity while maintaining top-notch results.
Machine Precision
While what can be achieved with hand-bent strips is limited, waterjetting can produce incredibly intricate designs with precision, our strip contractors tell us. When there is a need to standardize identical elements of a pattern, prefab strips are a speedy and straightforward way to do so.
Day explained that intricate designs and logos could be fabricated precisely, to within .005 of an inch, a degree of accuracy impossible to achieve by hand-bending from a diagram.
Design Desires
Prefab strips allow for third-party quality checks and review by all parties before production, noted Kevin Thornburg, Director of Design Engineering with Creative Edge Master Shop, a company specialized in architectural waterjet fabrication. NTMA divider strip manufacturers routinely send out drawings to be approved before cutting, so all involved are at ease.
Having been with his company for 14 years, Thornburg recalls that in his earlier years, only geometric shapes, without much detail, were possible with divider strips. With waterjetting, designs are increasingly more complex.
“More architects see that they can get the high-level design they want with terrazzo,” he said. “With waterjetting, we can get designers the desires of their hearts.”