Expanding the limits of design & quality and significantly reducing time & labor
Terrazzo artisans have a range of options to transfer a design to the floor. Some not only expedite and simplify the process—for cost savings—but can also provide a higher quality result and allow for a more complex design than can be achieved by hand. See how it’s done on several terrazzo Jobs of the Year.
The traditional system to execute a custom design in a terrazzo floor is to calculate the dimensions with CAD, then enter the field measurements into a shop drawing. With a grid drawn on the floor, the outlines can then be marked by hand on the floor. This system is still commonly used to lay divider strips for terrazzo.
“These terrazzo contractors are often fourth-generation terrazzo craftsmen, and it’s done truly craftsman style,” said Jim Thompson, executive vice president and commercial officer at Creative Edge. “Terrazzo artisans continue to successfully use this basic system to set strips by hand, just as it’s been done since the dawning of dividers strips, sometime before the 1890s.”
A great many terrazzo installations are simple, with straight lines and minimal patterning. For executing repetitive curves, some terrazzo contractors have built simple plywood templates to help lay the strips. Otherwise, there’s no call for a higher-tech solution to realize these types of design.
For more complex designs, however, it’s not the only option. The terrazzo industry offers a variety of solutions.
Prefabrication of elements
Prefabrication of complete terrazzo elements, such as base and stair sections, has been done since at least the 1920s in the artisan’s shop. Today, smaller complex designs, such as a logo or a decorative medallion, are also often precast, in whole or in part. Precast logos are more costly but provide greater flexibility for detailing.
Strip elements can also be formed by hand in the contractor’s shop and soldered to mesh for easy installation. On the 2018 Job of the Year, Texas Tech’s Amarillo Simulation Center, it was one of the artists, Brad Kaspari, who created the strip elements by hand in his studio.
Since waterjet technology reached the terrazzo industry in the 1990s, it’s been employed to produce design elements, whether strips or epoxy. Waterjet-cutting of strip designs is an option even for extensive patterning, as on the 2019 terrazzo Job of the Year: San Francisco’s Salesforce Transbay Transit Center.
When installers were asked to expedite the six-month installation schedule, they trimmed a month off while improving the quality of their installation by having the divider strips waterjet cut instead of shaping them by hand on-site. Panels as large as 11 by 17 feet were shipped and aligned on the construction site.
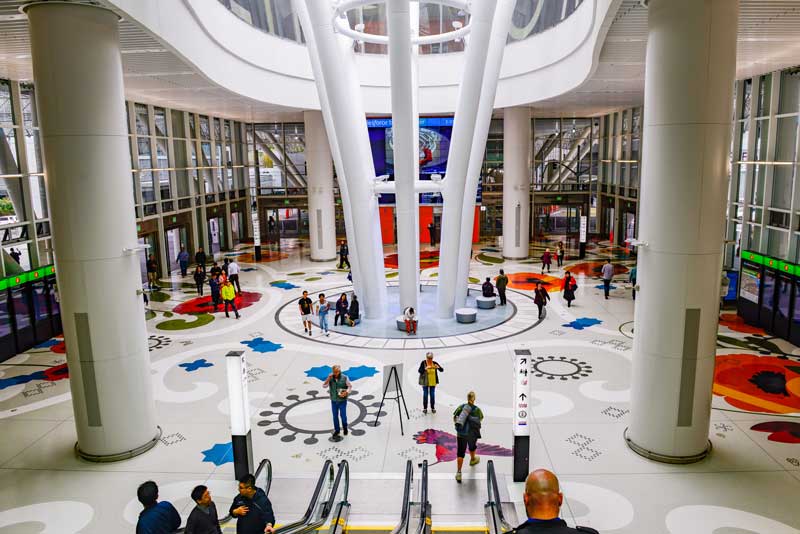
Stencils for design transfer
James Bateman, VP of the terrazzo division at Terrazzo & Marble Supply Company, is approaching 20 years in the industry. He reported that not much has changed in the industry during those years, other than stencil systems, which are typically used for strip layout. For a logo, unless it’s relatively simple, it’s generally more efficient to use waterjet, he said.
While stencils have been used over the past 10 to 15 years, Bateman revealed that their use has increased mainly over the last three to five years. Growing numbers of installers, who had been doing fine without them, are coming to discover the benefits.
“It’s pretty economical to get stencils and it saves a lot of labor,” he said.
Pittsburgh International Airport’s “Sky Beneath Our Feet” is the 2017 Job of the Year. The design process began with the artist’s drawings on paper, which were then traced into a CAD file and programmed into a waterjet. Approximately 70,000 square feet of templates were cut for the divider strip layout and then laid out along control lines in the terminal floor. The pattern was precisely reproduced and each section lined up to perfection through 60 distinct phases of the project.
“Stenciling is cost savings: purely time and labor,” Thompson said. “Especially for large jobs, reducing labor can have an enormous impact on the bottom line.”
How stencils work
The first step in producing terrazzo stencils is entering a custom design in a waterjet or ultrasonic machine, which cuts the design outline into interlocking sheets of heavy corrugated plastic foam board. Terrazzo artisans assemble the stencil sections on the floor like a puzzle.
The terrazzo contractor then paints the template lines, removes the stencils, inspects the layout, and applies the strips. This simple technology eliminates measuring and guesswork in transferring custom designs to the substrate.
The stencil material is durable enough to hold up on a construction site, and is often recycled as protection for the newly installed floor during work by other trades.
Beyond handcrafting
Thompson noted that sometimes a terrazzo design is beyond the reach of handwork in its complexity. So naturally, artists appreciate the advantage of the stencil system.
“The sky’s the limit with terrazzo design now, as well as with its color palette,” Thompson said. “There are still limits—you do have to be able to fit a chip in there—but we work with the designers and contractor to make a design as highly detailed as possible.”
A stencil system also ensures greater accuracy to execute an artistic vision onto the floor.
“Whatever’s programmed is what it will be,” Bateman explained. “It’s a fine line, because the guys who do this work by hand do it very well, but it’s almost foolproof with CAD drawings and waterjet.”
There may be no other field that so seamlessly blends technology, craftsmanship, and artistry.
“If a designer comes with a particularly complex design, instead of the installer telling them they can save money by limiting the strips, he may well be able to grant the designer’s wish, and at least as efficiently by using a stencil.”