How Terrazzo Won the Airport Bid Over an Ultra-Thin Option on Cost, Speed, Performance
In 2018-2019, Albany International Airport management was gearing up for major improvements. The base bid for flooring to replace carpet was for an ultra-thin manufactured terrazzo-style tile, seen as a budget-friendly option. However, before plans were finalized, the way was opened for a conversation about a poured-in-place thin-set epoxy terrazzo as an alternative to the bid.
Those weighing in on the terrazzo side included the architect, Michael W. LaMontagne, AIA, Principal Architect at C&S Companies in Syracuse, NY. Through multiple conversations, he recounted that airport representatives’ fears, based on several misconceptions about their options, were laid to rest.
Airport management thought there’d be more issues with terrazzo than with tiles, that the joints in the tiles would allow for more movement, while terrazzo would crack. They believed they would have more control and better color options with manufactured tile. They also thought it would be easier to phase the project with the tiles and keep the airport active during construction. “We had a lot of work to do,” Mr. Montagne recounted.
Thin-Set vs. Ultra-Thin
For several reasons, the facility owners settled on terrazzo as the better value. “Ultimately, the alternative was accepted because of notable cost savings on the bid,” Mr. LaMontagne said. Though they’d been led to believe an ultra-thin product would save money, they spent less on poured-in-place terrazzo than for tiles.
“First thing: you don’t save money even in the initial install with ultra-thin,” declared Michael Blackburn, Vice President, Sales & Marketing at Master Terrazzo Technologies in Levittown, PA. “And performance is lacking. Once a critical mass is reached in terrazzo, it is more cost-effective.”
Hand-Bent vs. Waterjet
Airport management had specified a highly patterned design for the floor. If ultra-thin terrazzo tile had been used, the patterns would have had to be outsourced to a waterjet company. One of the brands under consideration was about $30 per foot plus the costs of waterjetting. The advantage of terrazzo became clearer.
The terrazzo contractor quickly produced samples matched from the tile samples and could create the selected design by hand-bending the strips on site.
Another Deal-breaker: Lead Time
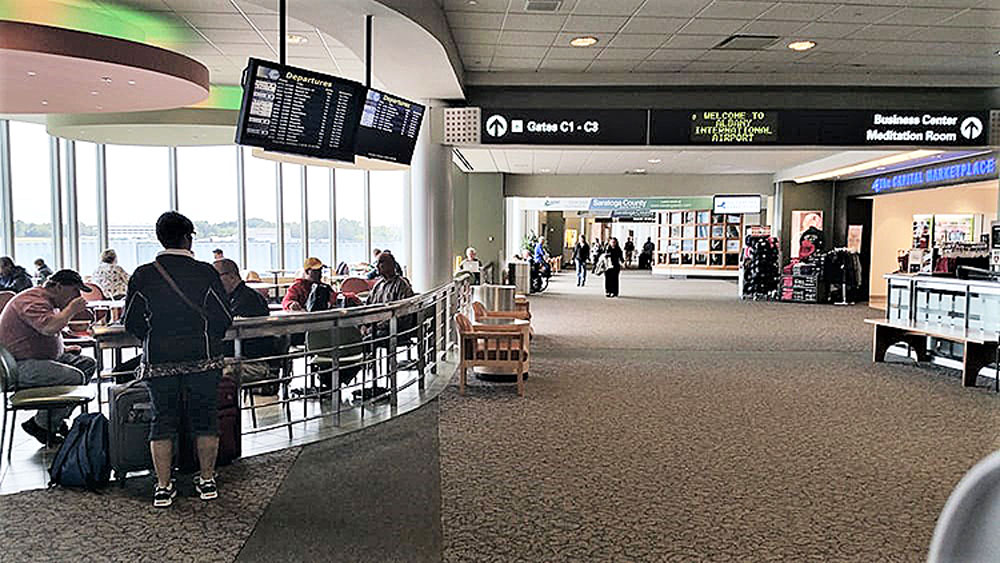
Comparing the lead time for each bid further simplified the decision. The tile manufacturer was crippled by a delay of at least two months before installation could begin due to the material’s production and delivery. The raw materials for terrazzo on the other hand, were on the job within two weeks. The job was finished more quickly than the tile was projected to be delivered.
Pictures Worth Thousands of Words
Mr. Blackburn said he had seen numerous examples of “massive issues” with ultra-thin tiles, including warping on the job site or after installation. Water seeping in later resulted in lippage and delamination. He shared photos of some of these instances with the client.
“I don’t have to search high and low for these examples,” he noted. “They’re more the rule than the exception.”
He also brought to the table the details from the literature and warranties of the manufactured systems.
“Poured-in-place terrazzo was a win on every metric,” said Mr. Blackburn. “The only reason to go thinner is cost savings, and it’s not worth what you give up. No question poured-in-place performs at a higher level than terrazzo-style tile. When presented honestly, it’s easy to see.”
One disadvantage of manufactured terrazzo-style tiles is the unavoidable joints. The seamless finish of poured-in-place terrazzo is far easier to maintain.
An example in point was seen at another New York State airport. While the rest of the floor was poured-in-place terrazzo, a white ultra-thin 2×2-foot format terrazzo-style tile was used in one terminal to save money.
Mr. Blackburn was called in later to check the floor and try to help them out of their predicament. He reported high foot traffic, and expansion and contraction, caused the grout joints to open up and turn dark. Cleaning machines only managed to pick up the dirt from the joints and spread it around.
“They can’t get it clean because it’s not monolithic,” Mr. Blackburn explained. “They deeply regret it.”
Seamless Advantage
Ultra-thin tiles installed with abutted joints lead to other problems, he continued. Cleaning chemicals seeping in leads to delamination and staining. Topcoats have to be stripped and reapplied.
“There’s nothing worse, especially with lighter color ultra-thin because of the grout joint problem,” Mr. Blackburn declared. “It’s the only floor product I speak out against this way. It offers no actual savings and is so clearly an inferior product.”
As is standard for an epoxy installation, Albany’s terrazzo included proper treatment of the substrate control joints and a full crack-suppression membrane. NTMA standard maintenance for poured-in-place terrazzo is inexpensive and simple, using an auto scrubber or mop and bucket.
Walk a Job
If you are looking for a product that is new on the market and may resemble poured-in-place terrazzo, “walk a few jobs,” advised Joe Iorio, Project Manager at Yorie Tile & Terrazzo of Allentown, PA, the terrazzo contractor at Albany. You can see how a product has worn over time and whether it will meet your expectations.
By careful phasing of the installation, Albany International continued operations during the terrazzo installation, as is standard in similar instances.
At Albany, the choice was clear: a lower bid number, shorter lead times, and quicker install. The result? A seamless, simple-to-maintain product that will equal the life cycle of the building.
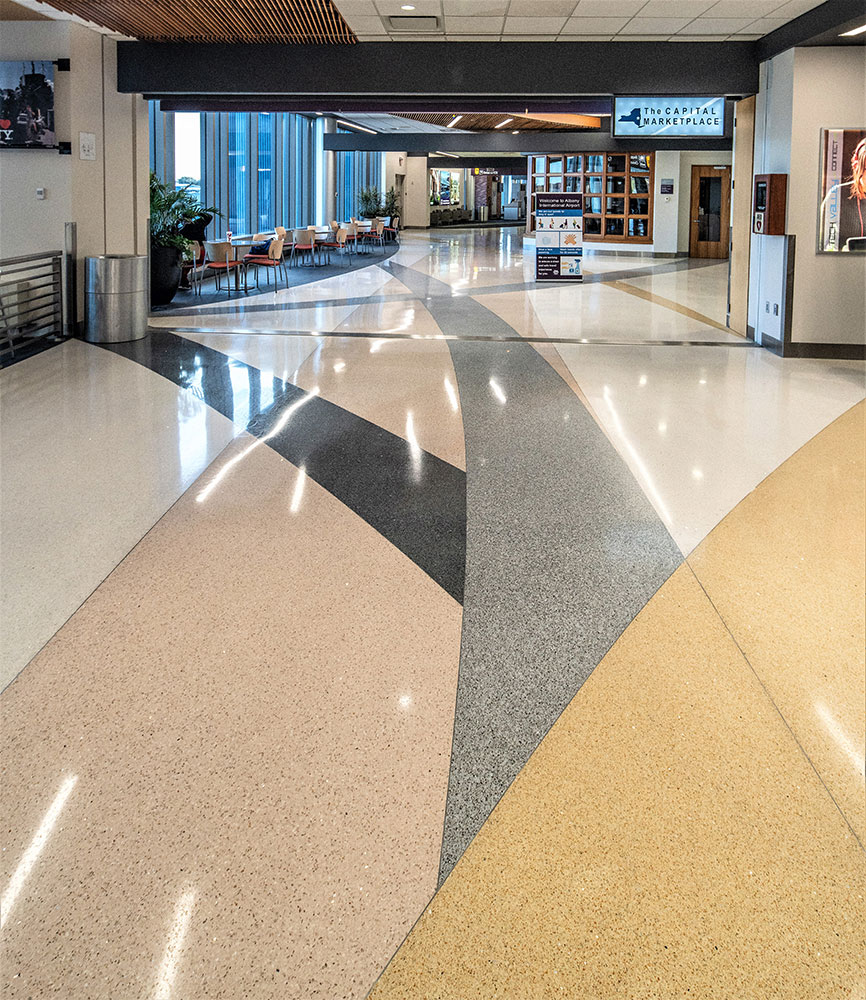